
読み物
Reading
セイルオンと機械製作
大量生産への第一歩
―機械製作事始め①
全て手作業のかいわれ大根作りの限界。
機械化を目指すが、問題は機械をどうやって準備するかだった。
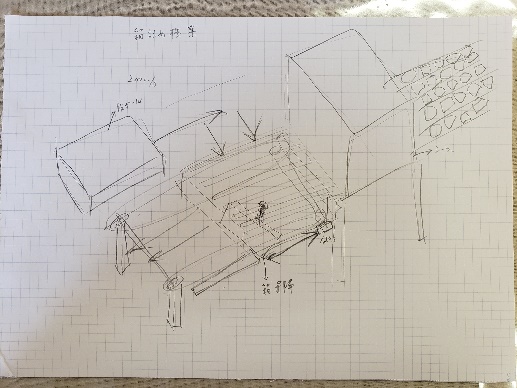
当社の特徴の一つが、本格的な機械製作を自前でやることです。
創業後、かいわれ大根の出荷量が次第に増えるにつれ、必然的に作業の効率化を意識するようになりました。そこで、何とか作業を機械化できないかと考えるようになったのが、機械製作のきっかけでした。
当時はまだかいわれ大根を作っている農家自体が少なく、播種(種まき)機や梱包機など、栽培・出荷に必要な機械をかいわれ大根専用に作っているメーカーはどこにもありませんでした。機械など自分で作ったこともなかったため、初めは大手機械メーカーに見積もりを依頼。しかし、一品物となる機械の見積もり額は約1,000万円を優に超えており、それに加えて開発過程で得られた知見は全てメーカーに帰属するという条件付きでした。
当時の売上はまだ2千万円~3千万円程度であり、到底手の届く金額ではありません。しかも、開発過程の知見などは手元に残らない。「それなら、自分で作るしかない。」自然とそう考えていたといいます。
とはいえ、いきなり機械が作れるわけでもなく、初めは地元の機械製作会社に頼んで作ってもらいながら、その過程でいろんなことを教わりつつ、納品された機械を見て改善点を考えるうちに、次第に少しずつ機械を作れるようになっていきました。
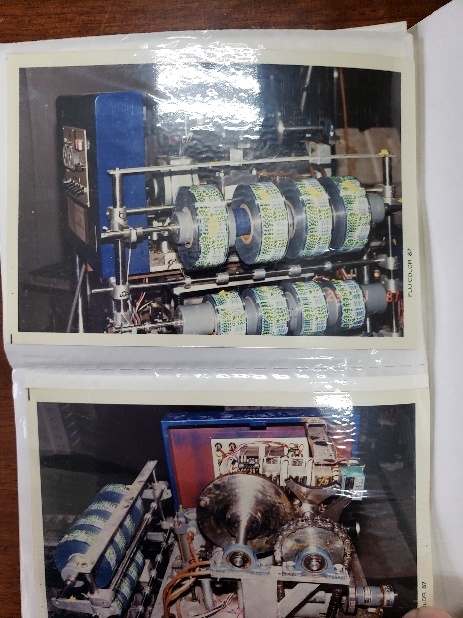
「ここはこうしたらいいんじゃないか?」と思ってやると、「あ、動いた。」そんなことの積み重ねで、本格的に機械を作るようになったのは、ウレタン培地で作ったかいわれ大根をパックに入れて出荷するようになってからでした。
振り返ってみると、当時作った機械は現在製作している機械に比べて機構が大変複雑でした。見た目がシンプルなものは作るのも簡単そうですが、実はいかにシンプルな機構にするかをゼロから設計して考えるのがとても骨を折る作業なのです。
当時の複雑な機構は、素人ながらもとにかく何とか動くものを作ろうと試行錯誤した結果でした。
農家が機械屋に
―機械製作事始め➁
かいわれ農家と機械屋の両立。
現在まで活躍している機械たちと支えてくれた人々との思い出。
機械を作るためには、機械を作るための機械、いわゆる工作機械が必要になります。本格的に機械を作ると決めてから、最初に買ったのは、旋盤でした。
それは恐らく1980年代半ば頃、当時出入りしていた工具屋さんに、「ベアリングのハウジングを作りたいんだけど、どうしたらいい?」と相談したところ、「それなら“旋盤”が必要です」と教わり、当時400万円ほどで購入。しかし、買ったのはいいものの、旋盤を触ったこともないので使い方が全く分かりません。「で、これどうやって使ったらいいの…?」と、買った後になって工具屋さんに聞くことに。
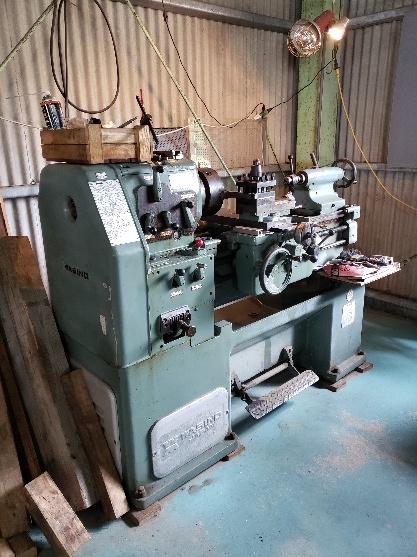
このときは、近郊の北九州市が製造業(鉄鋼)の街であったことが幸いし、購入した工具屋さんのつてで、引退した旋盤職人の方がわざわざ門司から岡垣まで通って、半年ほど扱い方を教えてくれました。なんとか旋盤は使えるようになったものの、旋盤だけでは作れる部品が限られてしまいます。やはり、機械を扱える従業員を雇わなければならない。ちょうどその頃に縁があって、他社でフライスの職人をしていた方がたまたま入社することになります。これが、現在に至るまで当社の機械製作の中核を担っている従業員さんとの出会いでした。
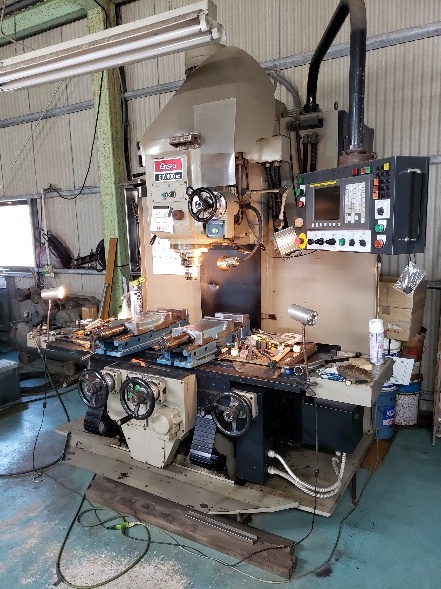
彼にどうやって機械を作ったらいいだろうかと相談したところ、「フライスやプラズマカッター、TIG溶接機なんかがあれば、もっと色んな部品が加工できて、機械が作れますよ。」と教えてくれました。そこで早速カタログを取り寄せ、どれがいいか思案した挙げ句、当時1,100万円ほどでフライスを購入。
さらにその後、貝割のカップを自社で真空成型するため、建物と合わせて約1億円を投じて真空成形機まで購入することになります。
傍からは、「あいつは機械を買い込んで何やってるんだ。」と言われたこともあったそうですが、「この決断があったからこそ、この会社はいまも生き残っていると思う。」と当時を振り返ります。
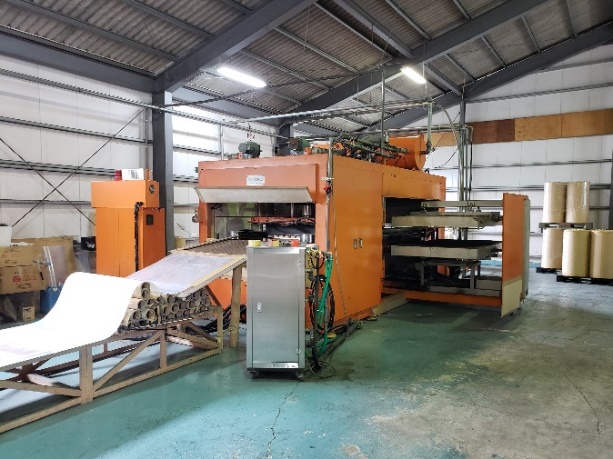
当社で製造するかいわれ大根の生産量は、年間約1,000万パックを越えます。最盛期は3000万パックを越えていました。1パックあたり1円のコストダウンができれば、年間で約1,000万円~3,000万円のコストダウンにつながります。そして、これが20年続けば2億円~6億円のコストダウンになります。販売単価がそう高くない野菜の生産においては、これだけコストダウンは相当なインパクトがあります。
そしてこの当時買った旋盤、フライス、真空成形機は、メンテナンスを重ねながら、いまも現役で動き続けています。これらの工作機械を使って、収穫機や播種機、栽培容器の洗浄機など、生産に必要な機械の大半を内製し、壊れたら自社で修理をする。機械にトラブルがあっても絶対に出荷を遅れさせない。そして、コストをできる限り抑える。この点で、機械作りが非常に役立っています。
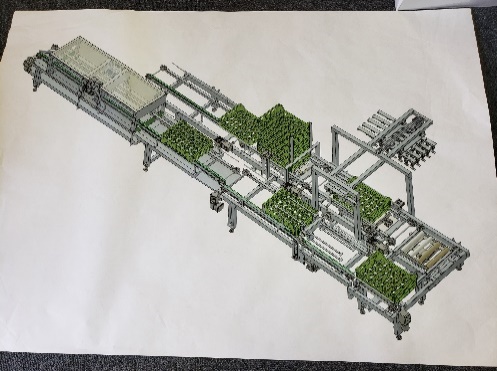
平成28年からは2D-3D CADを導入。より効率的で、衛生的な栽培工程を目指して、逐次機械の更改を進めています。
今後も、機械化による合理的な生産体制の整備と、良質なスプラウトを生産するための栽培ノウハウの積み重ねにより、お客様に安心していただける品質で商品を継続してお届けすること。これを目標として、日々邁進していきたいと思います。